PRECLEANER
When the conveyed ore is so sticky that it doesn’t fly off at the discharge pulley, normal scraper systems struggle to remove it from the belt. This usually means that the whole conveyor belt system gets clogged with carryback, and ends up with an unscheduled stop for cleaning. Tecnipak has developed a specialty precleaner that has been designed to cut through the thick layer of ore, releasing the bulk of the material from the belt, and allowing it to continue its journey through the chute.
The cleaning edge is composed of several blades placed next to each other, each of which have a beveled attack edge made from solid tungsten carbide blocks and a ceramic layer that protects the frame of the precleaner from wear. There is no other cleaner in existence capable of dealing with the impact and abrasion that results from the removal of the bulk of the conveyed ore.
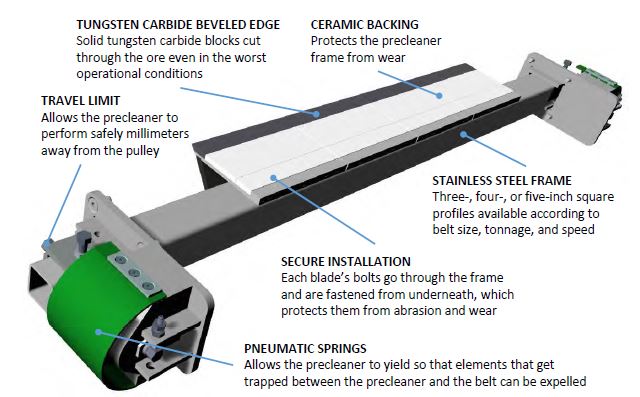
TRAVEL LIMIT
Allows the precleaner to perform safely millimeters away from the pulley.
TUNGSTEN CARBIDE BEVELED EDGE
Solid tungsten carbide blocks cut through the ore even in the worst operational conditions.
CERAMIC BACKING
Protects the precleaner frame from wear.
PNEUMATIC SPRINGS
Allows the precleaner to yield so that elements that get trapped between the precleaner and the belt can be expelled.
SECURE INSTALLATION
Each blade’s bolts go through the frame and are fastened from underneath, which protects them from abrasion and wear.
STAINLESS STEEL FRAME
Three-, four-, or five-inch square profiles available according to belt size, tonnage, and speed.
• Specialty cleaner. Designed to improve cleaning when the bulk of the conveyed ore doesn’tfly off the discharge pulley, the precleaner cuts through the bulk and allows for the primarycleaner to perform in normal conditions. Highly favored in leaching operations where theore is particularly cohesive and sticky, there is no other cleaner that works as efficiently andreliably in these conditions.
• Tough. The frame is made from a three-, four-, or five-inch stainless steel square profile withthicknesses from 1/4“ to 3/8”. Tecnipak guarantees that it will withstand even the mostaggressive mine duty.
• Pneumatic springs safety mechanism. The precleaner works millimeters away from thedischarge pulley and has pneumatic springs that allow it to yield so that any elements thatget trapped between the belt and the precleaner are expelled.
• Remote adjustment. The adjustment controls can be installed in a safe place, away from thehazard zone, which allows the precleaner to be adjusted while the belt is running.
• All-around reliability. Every part has been designed and developed to perform with minimalmaintenance and a wide tolerance to changes in the working conditions.
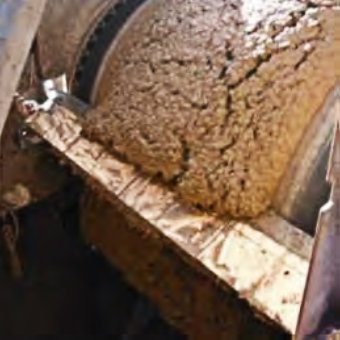
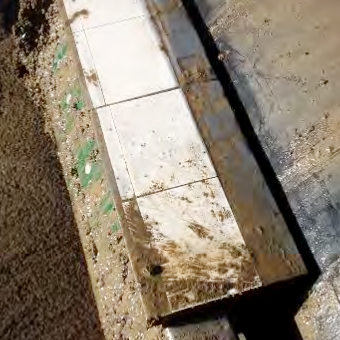
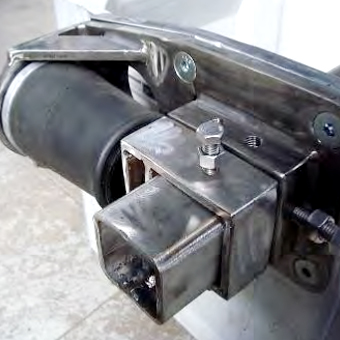
SPECIFICATIONS:
- Belt speeds up to 7.5 m/s (1,450fpm)
- Belt widths from 900 mm up to3,150 mm (36’’ up to 124’’)
- Pulley diameters from 800 mm up to 3,000+ mm (32’’ up to 118+’’)
WORKING PRINCIPLE
1. The cleaning edge is composed of several blades, each with a tungsten carbide beveled edge that is adjusted so as to be a few millimeters away from the pulley.When the moving ore encounters the precleaner, the cleaning edge cuts through the ore and hence detaches the bulk of the conveyed material so it can be driven into the chute.
2. Once the bulk of the ore has been detached, the precleaner has to redirect the ore over the precleaner and into the chute. This exerts a great force on the surface ofthe blades, which also generates an important abrasion stress. Ceramic tiles withstand the abrasion while at the same time pass down the force onto the framebeing held by the adjustment consoles through the pneumatic springs.
3. Finally, the ore is clear from the precleaner and continues its journey through the chute. Over the belt remains a thin layer of ore, which is later removed by the primary and secondary cleaners.
PNEUMATIC SPRINGS SAFETY MECHANISM
In cases where a rock gets jammed between the precleaner’scleaning edge and the pulley, it is necessary that the rock can be released to avoid damage to the belt.
Thanks to the pneumatic spring safety mechanism, when a rock gets stuck and the pulley pushes it further between the pulley and the cleaning edge, the frame of the precleaner yields.
The pneumatic springs absorb the displacement of the precleaner until the rock is expelled, at which point the springs restore the precleaner to the working position.
All of this happens in a fraction of a second, so the cleaning quality is never impaired.
Which precleaner size should I choose? The precleaner should wipe the entire width of the belt, so it should have the same width as the belt.
At what angle should the precleaner be installed? The precleaner must be installed with an installation drawing supplied by Tecnipak for each particular installation. However, it is desirable that it operates between 25 to 45 degrees from a horizontal plane.
The blades in the center wear out faster than the ones on the sides. What should I do? This behavior is normal and should be expected, because the bulk of the load travels centered on the belt and this wears down the blades on the center faster. To make the blades last longer, when the center blades are worn, a rotation should be performed in which the center blades take the place of the outer blades and vice versa. For more information, please review the manual or give us a call.
SAFETY WARNING: the installation of a precleaner demands that the belt has fully operational return cleaners. The pulley should be centered and its lagging should be in good shape; and the belt must not have mechanical splices, protruding splices, protruding cords, or other protruding elements. Dismissing this safety warning may cause damage to the belt, other equipment, or people.
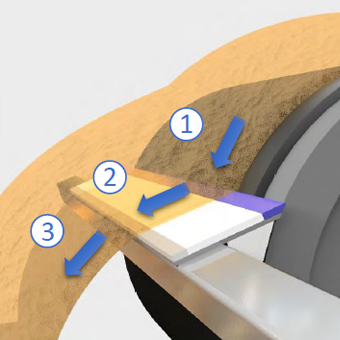
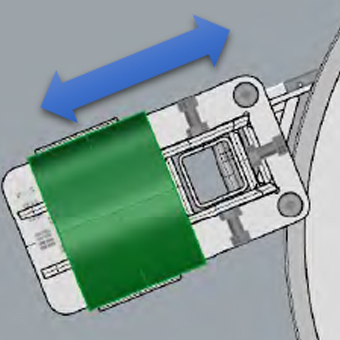
Which precleaner size should I choose?
The precleaner should wipe the entire width of the belt, so it should have the same width as the belt.
At what angle should the precleaner be installed?
The precleaner must be installed with an installation drawing supplied by Tecnipak for each particular installation. However, it is desirable that it operates between 25 to 45 degrees from a horizontal plane.
The blades in the center wear out faster than the ones on the sides. What should I do?
This behavior is normal and should be expected, because the bulk of the load travels centered on the belt and this wears down the blades on the center faster. To make the blades last longer, when the center blades are worn, a rotation should be performed in which the center blades take the place of the outer blades and vice versa. For more information, please review the manual or give us a call.
SAFETY WARNING: the installation of a precleaner demands that the belt has fully operational return cleaners. The pulley should be centered and its lagging should be in good shape; and the belt must not have mechanical splices, protruding splices, protruding cords, or other protruding elements. Dismissing this safety warning may cause damage to the belt, other equipment, or people.
PRIMARY BELT CLEANER
Tecnipak’sprimary belt cleaner is designed to remove the thick layer of carryback material that remains stuck to the conveyor belt after its discharge. This is the sturdiest and toughest primary belt cleaner available, developed after years of experience in the harshest operational conditions in the Chilean mining industry. The cleaning blade is made out of a polyurethane formulation with the best combination of wear, tear, and corrosion resistance.
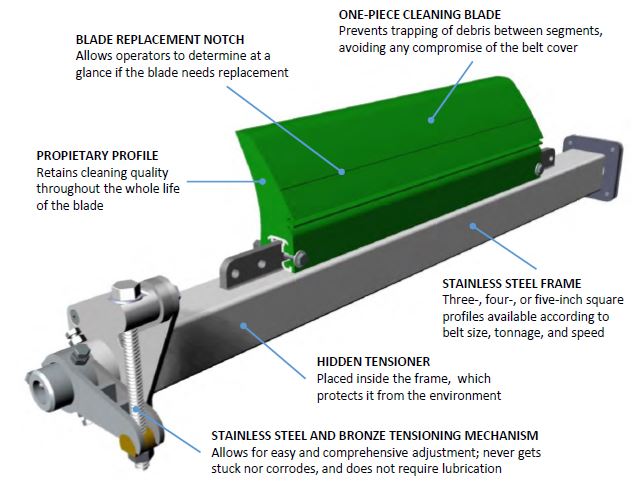
PROPIETARY PROFILE
Retains cleaning quality throughout the whole life of the blade.
BLADE REPLACEMENT NOTCH
Allows operators to determine at a glance if the blade needs replacement.
ONE-PIECE CLEANING BLADE
Prevents trapping of debris between segments, avoiding any compromise of the belt cover.
STAINLESS STEEL AND BRONZE TENSIONING MECHANISM
Allows for easy and comprehensive adjustment; never gets stuck nor corrodes, and does not require lubrication.
HIDDEN TENSIONER
Placed inside the frame, which protects it from the environment.
STAINLESS STEEL FRAME
Three-, four-, or five-inch square profiles available according to belt size, tonnage, and speed.
• Toughest cleaner available. The frame is made from a three-, four-, or five-inch stainlesssteel square profile with thicknesses from 1/4“ to 3/8”. Tecnipak guarantees that it willwithstand even the most aggressive mine duty while delivering excellent cleaningperformance.
• Single-side tension adjustment. The tensioner relies on a simple, easy-to-understandmechanism that is adjusted from just one side, reducing the time needed for cleaner setup.Built entirely in stainless steel and bronze, the mechanism doesn’t get stuck, corrode, orneed lubrication.
• Installation closer to the pulley. Tecnipak’sproprietary blade profile allows for aninstallation closer to the head pulley, reducing the risk for the cleaner to flip over when thecleaning blade is wearing out.
• Wear-, tear-, and acid-resistant polyurethane. The formulation for our 83 Shore A hardnesspolyurethane blade offers the best compromise between wear, tear, and corrosionresistance. Tecnipak can also supply different formulations for specific conditions.
• All-around reliability. Every part has been designed and developed to perform with minimalmaintenance and a wide tolerance to changes in the working conditions.
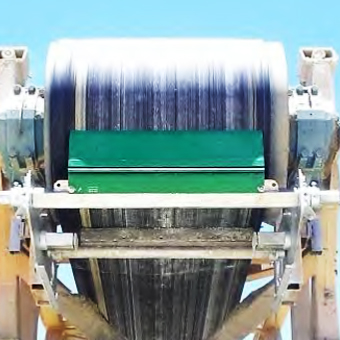
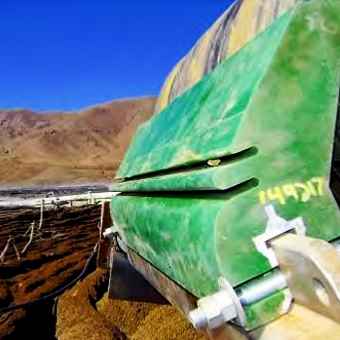
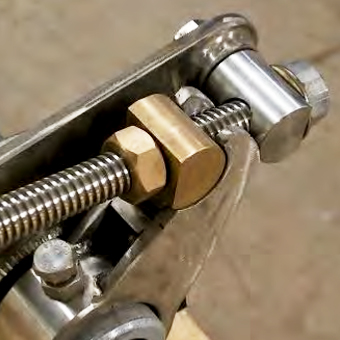
SPECIFICATIONS:
- Belt speeds up to 7.5 m/s (1,450fpm)
- Belt widths from 600 mm up to3,000 mm (24’’ up to 120’’)
- Pulley diameters from 400 mm up to 3,000+ mm (16’’ up to 120+’’)
Which blade length should I choose? The blade width normally ranges from 75% to 80% of the belt width. On occasions, a larger or smaller size should be used, matching the width of the ore path on the belt cover. A blade that is too small will let ore pass through the sides. A blade that is too large will wear only in the midsection and not on its edges.
As the blade wears out my belt cleaner flips over. What is the problem?The cleaner is installed too far away from the pulley. It is necessary to check the positioning, relocate and reinstall.
The cleaning blade lasts less than 15 days. What can I do? Contact Tecnipak. It is likely that you are facing a special condition where the ore does not fly off the belt when it reaches the head pulley, but rather sticks to the belt. In this particular case it might be necessary to install a Tecnipak precleanerabove the primary cleaner.
RETURN BELT CLEANERS
Tecnipak’sprimary belt cleaner is designed to remove the thick layer of carryback material that remains stuck to the conveyor belt after its discharge. This is the sturdiest and toughest primary belt cleaner available, developed after years of experience in the harshest operational conditions in the Chilean mining industry. The cleaning blade is made out of a polyurethane formulation with the best combination of wear, tear, and corrosion resistance.
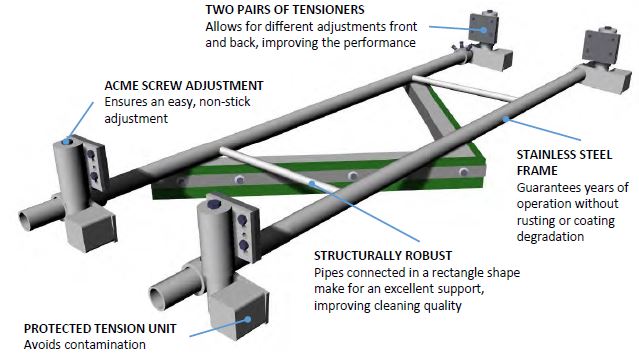
PROTECTED TENSION UNIT
Avoids contamination.
ACME SCREW ADJUSTMENT
Ensures an easy, non-stick adjustment
TWO PAIRS OF TENSIONERS
Allows for different adjustments front and back, improving the performance.
STRUCTURALLY ROBUST
Pipes connected in a rectangle shape make for an excellent support, improving cleaning quality.
STAINLESS STEEL FRAME
Guarantees years of operation without rusting or coating degradation.
• Tensioning consoles. Tecnipak’sreturn belt cleaners have telescopic tensioning consolesthat allow the cleaning blades to be applied directly onto the belt, so that they can reallyperform and push against the return belt for better cleaning.
• Polyurethane blade. The blade is made out of 83 Shore A hardness polyurethane, which hasa much lower sliding resistance against the belt than blades made out of rubber that areusually used in these types of cleaners. Because of this, it is friendlier to the conveyor beltsystem while at the same time improving the cleaning quality.
• Toughest cleaners available. Tecnipak manufactures the frame of our return cleaners in 2’’,2½’’, and 3½’’ pipe. They are the toughest cleaners available, and by making them instainless steel, we can guarantee their performance even in the worst conditions.
• Square-in-square elastomer. The element that delivers the tension is a square-in-squareelastomer that acts as a pivot point for the lever arm. This way the tensioner can absorb deviations in the operational conditions, such as splices, misalignment, and repaired belts.
• ACME screw adjustment. The tension consoles have an ACME threaded screw that runs onthe inside of the telescopic system for adjustment. This enables it to be adjusted easily andwithout the need for special tools.
• V-Plow or diagonal. Install a v-plow cleaner for optimal performance, or a diagonal cleaner ifoperational conditions require the ore to be removed only towards one side of the belt.
• All-around reliability. Every part has been designed and developed to perform with minimalmaintenance and a wide tolerance to changes in the working conditions.
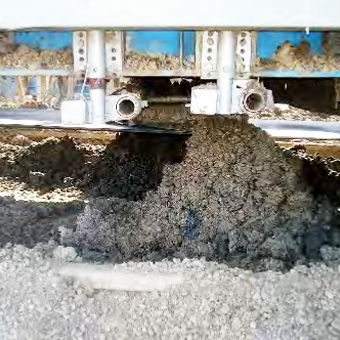
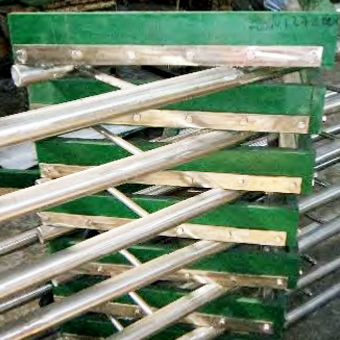
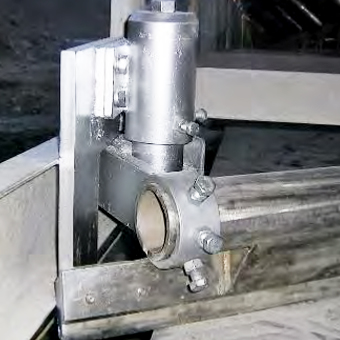
SPECIFICATIONS:
- Belt speeds up to 7.5 m/s (1,450fpm)
- Belt widths from 600 mm up to3,000 mm (24’’ up to 120’’)
Why are Tecnipak’sreturn belt cleaners more effective? Return belt cleaners that rest over the belt only exert a force over it because of their weight. This is not effective because the vibrations of the belt make these kind of cleaners vibrate on their own, at times separating them from the belt, which is why they let material through. In addition, they cannot remove ore that has stuck to the belt because they lack the necessary tension to do so.
Tecnipak’sreturn belt cleaners have tensioners that allow the cleaners to be applied directly against the belt, so that they can truly clean the return belt cover.
This is why even if the belt vibrates, Tecnipak’scleaners will not let ore pass through and will remove ore even if the material is stuck to the belt. It is for these reasons that Tecnipak’sreturn belt cleaners offer dramatically better cleaning quality than those from the competition.
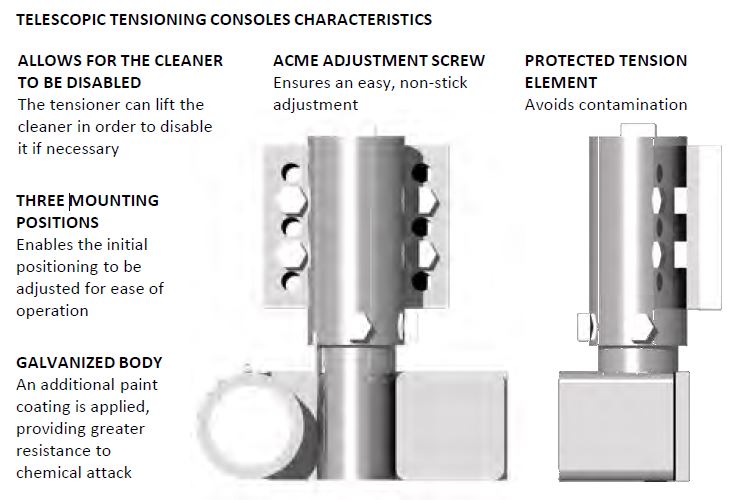
Should I choose a v-plow or a diagonal return cleaner?
The v-plow is the most efficient cleaner when it comes to protecting the tail pulley from the material that ends up on the inside of the return belt. Thanks to its V shape, the material is pushed quickly to both sides of the belt. The diagonal cleaner, on the other hand, works by pushing the material to just one side of the belt. This is an advantage when pushing the material to both sides is not an option, as can happen in underground mining, for example. So a v-plow should always be favored over a diagonal cleaner, whereas the latter should be installed if a v-plow is not an option.
SECONDARY BELT CLEANERS
Tecnipak’s secondary straight belt cleaner is placed right after the primary cleaner, underneath the head pulley, and is designed to clean fine particles off the conveyor belt. It is supported by pneumatic tensioners that work alongside the most durable cleaning blade in the industry so as to deliver the best cleaning quality, bar none. Additionally, for conveyor belts particularly long and fast, we’ve also developed a secondary parabolic belt cleaner that allows for focused cleaning performance.
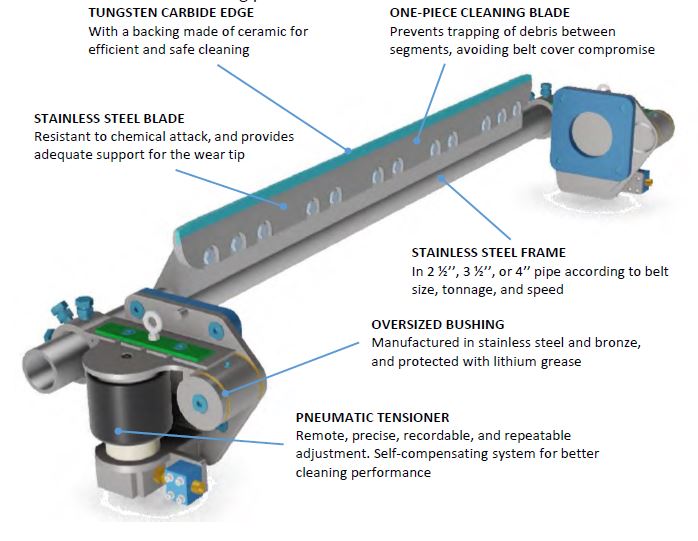
STAINLESS STEEL BLADE
Resistant to chemical attack, andprovides adequate support for the wear tip.
TUNGSTEN CARBIDE EDGE
With a backing made of ceramic for efficient and safe cleaning.
ONE-PIECE CLEANING BLADE
Prevents trapping of debris between segments, avoiding belt cover compromise.
STAINLESS STEEL FRAME
In 2 ½’’, 3 ½’’, or 4’’ pipe according to belt size, tonnage, and speed.
OVERSIZED BUSHING
Manufactured in stainless steel and bronze, and protected with lithium grease.
PNEUMATIC TENSIONER
Remote, precise, recordable, and repeatable adjustment. Self-compensating system for better cleaning performance.
• Safe for the conveyor belt. The one-piece cleaning blade avoids debris getting trapped, andits surface acquires a mirror-finish quality as it wears out so there is no danger of damagingthe conveyor belt.
• Unique wear parts. Tungsten carbide with great hardness and toughness, of our ownformulation, working with a black ceramic backing. This combination delivers exceptionaland long-lasting cleaning performance.
• Toughest cleaners available. Tecnipak manufactures the frame of our secondary cleaners in2½’’, 3½’’, and 4’’ pipe. They are the toughest belt cleaners available and because they aremade from stainless steel, we can guarantee their performance even in the worstconditions.
• Pneumatic tensioners. The tensioners share the same pneumatic circuit so they are self-compensating (if one side is more demanded, the opposite side adjusts automatically tocompensate). The cleaner’s adjustment is simple and because it can be narrowed down to apressure reading, it is precise, reliable, recordable, and repeatable.
• Remote adjustment. The remote adjustment box can be installed in a safe place, away fromthe hazard zone, which allows the belt cleaner to be adjusted while the belt is running.
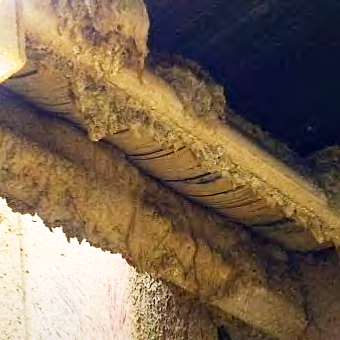
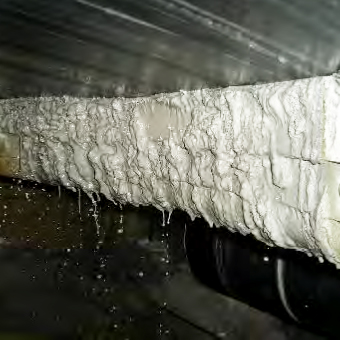
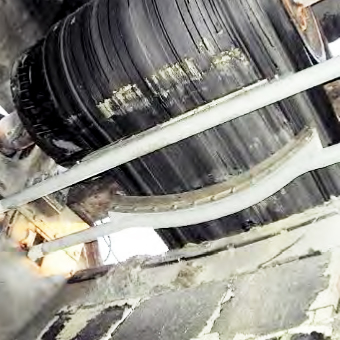
SPECIFICATIONS:
- Belt speeds up to 7,5 m/s (1.450fpm)
- Belt widths from 600 mm up to3.150 mm (24’’ up to 124’’)
- Pulley diameters from 400 mm up to 1.800 mm and above (16’’ up to 72’’+)
WORKING PRINCIPLE
The secondary straight belt cleaneris the main belt cleaning agent, and should be installed immediately after the point where the conveyor belt no longer touches the head pulley. It is at that spot that the maximum cleaning performance is achieved, while at the same time it is also the place where the removed material is most easily conveyed through the chute onto the next belt.
Tecnipak’s secondary cleaners, through their pneumatic tension system, keep the cleaning blade in contact with the belt at all timeswhile exerting an even, constant force against it. The pneumatic springs deliver the pressure that creates the force against the belt, and because they share the same pneumatic circuit, they are self-compensating: when the working conditions change, both sides work together to adjust to the new condition. The force that the tensioners exert on the belt is simple to calculate since it is just a function of the pressure of the pneumatic springs (as can be seen in the adjacent chart), and this makes it easy to work with the cleaner because you only need a single parameter that is recordable and repeatable to set up the cleaner. The adjustment controls are to be installed away from the hazard zone, which allows for the cleaner to be adjusted on-the-fly, even if the belt is running.
The secondary parabolic belt cleaneris used on long and fast conveyor belts, where the conveyed ore sticks strongly particularly on the center of the conveyor belt cover because of the troughing angle of the idlers. Because of this, it is necessary to add an extra belt cleaner capable of performing a cleaning job focused on the center of the belt. Thanks to its parabolic shape and the pivoting motion of the tensioner, the parabolic cleaner concentrates the force on the center of its blade, effectively delivering a focused cleaning job where it is most needed.
CLEANING BLADES TECHNOLOGY
Our standard cleaning blades are manufactured with a stainless steel body onto which the wear elements are affixed. The wear tip is made out of tungsten carbide and black ceramic: the carbide offers hardness, toughness, and guarantees a sharp edge for great cleaning quality, and the ceramic complements the carbide by increasing the contact area, which enhances durability and makes for a safer operation.
Besides our standard carbide-ceramic blade, we offer other formulations such as a carbide-only blade, a ceramic-only blade, or a polyurethane-blade, the latter of which is fully manufactured in Shore 83 A hardness polyurethane, for use in belts with cover damage or mechanical splices. All of our blades are fixed to the frame with standard stainless steel bolts, for installation and removal without the need for special tools.
PRESSURE ADJUSTMENT SYSTEMS
Our cleaners are supplied with a remote pressure adjustment box that can serve up to two cleaners. To inflate the pneumatic tensioners, it is necessary to have either a pneumatic circuit available with sufficient pressure or a portable wireless air compressor (supplied as standard).
Alternatively, we can supply a box with a high-pressure cylinder that also serves up to two cleaners, thanks to which bringing the cleaners to working pressure after maintenance is almost instantaneous.
It also absorbs the small leaks inherent to every pneumatic system, thus decreasing the maintenance frequency. This system can also be connected to an online platform, so that the monitoring and operation of the scrapers can be done remotely.

ADDITIONAL ALTERNATIVES
Tecnipak is continuously working on improving our scraper systems. We offer various alternatives to suit your particular working conditions, and we are experts in the design, development, manufacturing, and implementation of tailor-made solutions. Some of these solutions have become widely recognized by our customers, and we offer them as alternatives designed to suit specific requirements.
FULLY MECHANICAL TENSIONERS
For those customers who favor mechanical adjustment tensioners, Tecnipak has developed a tensioner with full mechanical operation. The frame is supported by a swing arm system which in turn slides along an ACME screw for regulation. Adjusting the tensioner is as easy as turning a nut and the swing arm system will slide up or down.
The tension is delivered by a square-in-square torsional elastomer that acts both as a spring and damper, so that the scraper will not achieve resonance when it is subjected to the vibrations inherent in a conveyor system.
The construction of the tensioner is in full stainless steel with the exception of the bushing of the thread, which is manufactured in brass to prevent the mechanism from getting stuck. All of the above guarantees that the tensioner is extremely reliable.
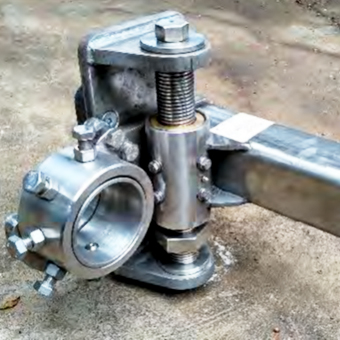
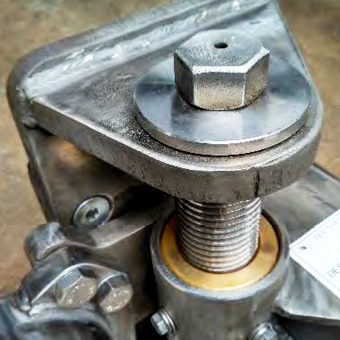
PROFILE BLADE
Tecnipak’s standard straight blade delivers stunning cleaning quality on most conditions; however, when the lining of the head pulley is very worn, when the belt shows heavy wear on its center, or when the belt has too much “memory" and is not straight enough after going through the head pulley, the standard straight blade may have problems delivering a good cleaning.
To correct this situation, Tecnipak recommends the use of a profile blade which compensates for these deviations, and ensures that the blade makes appropriate contact with the belt. The exact shape and rise of the profile will depend on the conditions of each conveyor system, so Tecnipak first gathers the necessary information from the conveyor system and then proceeds to make a tailored design and manufacture a specific profile blade for the application.
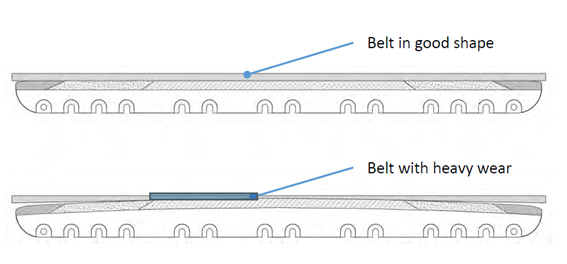
SPEED-CHANGE SECONDARY SCRAPER
For customers who value safety and efficiency, Tecnipak manufactures a speed-change secondary scraper that enables the customer to quickly and efficiently replace a worn blade.
Designed to save time and ensure a safer operation, this equipment prevents maintenance teams from getting inside the chute to change blades, where the working conditions are harder and with greater exposure to risk. Instead, after the tension has been removed, the scraper is released and pulled from the side of the chute and slides to a safe maintenance position. This whole maneuver is carried out from outside the chute, and allows for the maintenance staff to perform a blade replacement in a comfortable and safe manner.
Once the blade replacement is done, the scraper slides back into working position, is properly secured, and the tension is reapplied so that the scraper can continue its operation.
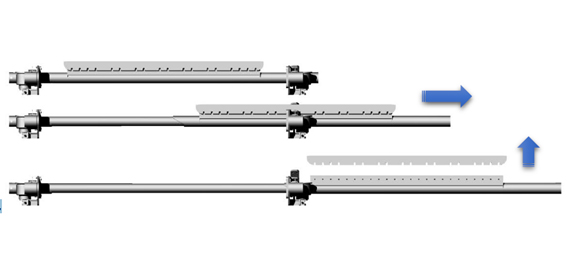
POLYURETHANE COATING
In places where the acidity in the conveyed ore is extreme, there is the possibility that even stainless steel does not offer adequate protection from corrosion. For these conditions, Tecnipak can coat the frames of its scrapers with a polyurethane coating. Thus the scraper’s frame gets an additional layer of protection against acid, increasing the life span of the equipment in these adverse conditions.

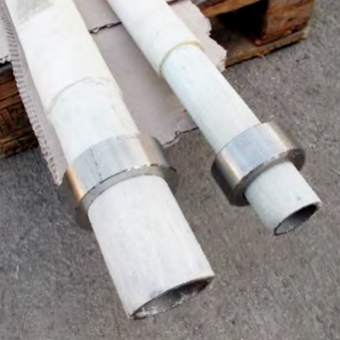
Belt cleaner placement:
- Determine the belt width.
- Locate distances “A” and “B” from the reference table (right).
- Identify the point at which the belt no longer touches the head pulley and fromthat point, measure distance “A” in the direction of the belt (a range is allowed to avoid inferences,as indicated on the table).
- Trace distance “B”perpendicular to the belt.This is the distance between the belt cover and the axis of the frame.
- Install the tensionerwith its arm parallel to the belt, asshown.

Which blade size to use?
Each cleaner has its own blade. The length of the blade should match the width of the belt, as a shorter blade will not be able to clean the far ends of the belt and a longer blade will not wear out on its ends, which could damage the belt.
The belt is coming out clean on one side but dirty on the other. What can I do?
Uneven cleaning is the result of the cleaner being unevenly applied on the belt. Check that the movement of the cleaner is unencumbered and that its travelling path is clear. If that does not resolve the issue, check the position of the tensioners to ensure that the belt cleaner is properly aligned.